Home » Solar Basics » Solar Cell Manufacturing Process
Solar Cell Manufacturing Process
Solar cells are made of various materials, the most common of which include silicon, indium gallium, cadmium selenide, etc. These materials play a vital role in the manufacturing process of solar cells. Silicon is one of the most commonly used solar cell materials at present. It has good semiconductor properties, can generate electron-hole pairs under light and convert them into electrical energy, and has high photoelectric conversion efficiency and stability. Currently, the main types of solar cells include silicon crystal solar cells, thin film solar cells, and some emerging solar cells. The manufacturing processes of various solar cells are constantly being optimized and innovated to improve efficiency, reduce costs, and enhance the stability and durability of the cells. With the advancement of science and technology, new manufacturing technologies and materials may emerge in the future, promoting further innovation in solar cell technology.
All About Silicon
The Silicon Atom
Silicon (Si) is a very abundant nonmetallic element that makes up about 26% of the earth's crust and is the second most abundant element after oxygen. It is also the 7th most common element in the universe. Silicon is usually found in the form of silicon dioxide, usually known as quartz. As depicted in the diagram, the silicon atom has 14 electrons. Electrons that are further from the nucleus have more energy than electrons closer to the nucleus. The four electrons that orbit the nucleus in the outermost energy levels, valence electrons, are the ones that interact with neighboring atoms to form solids. In silicon solids, each silicon atom shares one of its four valence electrons with each of four neighboring atoms. Only the outermost four electrons can be given to, accepted from, or shared with other atoms. These valence electrons, play a very important role in the photovoltaic (PV) effect.
The Silicon Lattice
Large numbers of silicon atoms bond with each other using their valence electrons to form a crystal. The two-dimensional diagram is a simplified two-dimensional picture of silicon crystal. The actual crystal is a more complicated three-dimensional structure. Silicon crystal consists of "units of five silicon atoms" - the original atom plus the four other atoms with which it shares valence electrons. This repeated atom pattern is known as the silicon lattice. Pure silicon is a very poor conductor of electricity, but when certain impurities are added (called "doping") its electrical characteristics are greatly enhanced. Hence the name "semiconductor". Under certain conditions silicon conducts electricity and under other circumstances, it doesn't. Solar cells using this technology are referred to as crystalline silicon cells.
Creating Silicon Wafers
Almost all of the silicon crystals grown for solar cells are produced by the Czochralski process (invented in 1916 by the Polish chemist Jan Czochralski, pronounced Cho-crawl-ski). Very high purity, 99.9999% pure, semiconductor-grade silicon (a few parts per million of impurities) is required for solar applications. The process begins when the production chamber is heated to approximately 1500 degrees Celsius to melt raw silicon in a crucible. Small precise amounts of impurity atoms such as boron or phosphorus are added to the molten silicon in order to dope the silicon, changing it into n-type or p-type silicon.When the silicon is fully melted, a small precisely oriented seed crystal mounted on the end of a rotating shaft is slowly lowered until it just dips below the surface of the red-hot molten silicon. The shaft rotates counter-clockwise and the crucible rotates clockwise. The rotating rod is then drawn upwards very slowly, allowing an ingot to be formed. By precisely controlling the temperature gradient, rate of pulling, and speed of rotation, a large, "single crystal", cylindrical ingot is extracted from the melt.
The ingot can be one to two meters in length depending on the amount of silicon in the crucible. This process is normally performed in an inert atmosphere, such as argon, and in an inert chamber. A cutting machine designed to slice very hard silicon uses a multi-wire diamond saw. This device is especially important in the silicon solar cell industry to cut the ingots into very thin wafers 200 microns (millionths of a meter) or so thick, and some as thin as 160 microns. These extremely thin wafers are very brittle and are easily broken. Extreme care is necessary in the handling of these wafers to prevent damage.
Crystalline Silicon Solar Cells
The Photovoltaic Effect
The PhotoVoltaic (PV) effect is the process by which a PV cell converts sunlight into electricity. When light shines on a PV cell, the radiation may be reflected, absorbed, or passed right through. But only the absorbed light generates electricity. The energy of the absorbed light is transferred to electrons in the atoms of the PV cell. With their newfound energy, these electrons escape from their normal positions in the atoms of the semiconductor material and become part of the electrical flow, or current, in an electrical circuit. A special electrical property of a PV cell - called the "built-in electric field" - provides the force, or voltage, needed to drive the current through an external load, such as a light bulb.
To induce the "built-in electric field" within a PV cell, two layers of differing silicon are placed in contact with one another. One layer is an "n-type" material with an abundance of electrons, which have a negative electrical charge. The other layer is a "p-type" material with an abundance of "holes," which have a positive electrical charge. The top layer is "doped" with phosphorus, which bonds with the silicon to create a negative charge (extra electrons). The bottom layer of the PV cell is usually "doped" with boron, which bonds with the silicon to create a positive charge (extra holes).
The "dopant," which is the introduced element, has either three or five valence electrons—which is one less or one more than silicon's four. Substituting a phosphorus atom (with five valence electrons) for a silicon atom in a silicon crystal leaves an extra unbonded electron that is relatively free to move around the crystal. Substituting a boron atom (with three valence electrons) for a silicon atom in a silicon crystal leaves a hole (missing electron) that is relatively free to move around the crystal.
When n- and p-type silicon come into contact, the two semiconductors behave like a battery, creating the "built-in electric field", or voltage, at the surface where they meet called the "p/n junction". The voltage causes electrons to move towards the negative surface, where they become available to the external electrical circuit. At the same time, the holes move in the opposite direction, toward the positive surface, where they await incoming electrons. When the sun's photons enter the semiconductor, some of the photons with the "right amount" of energy collide with atoms, and free negative electrons and free positive holes are created. The "right amount" of energy is called the "band gap" energy and it varies from one semiconductor material to another. Given the electric field, the free negative electrons go in one direction and the free positive holes go in the other creating a current of electricity. The p/n junction is the key instrument in the creation of electricity by a solar cell.
Crystalline Silicon Cell Structure
A typical solar cell consists of a glass or plastic cover, an anti-reflective layer, a front contact to allow electrons to enter a circuit, a back contact to allow them to complete the circuit, and the semiconductor layers where the electrons begin and complete their journey.
The most important parts of a solar cell are the semiconductor layers. This is where electrons are freed and the electric current is created - it's the active layer. When sunlight enters the cell, its energy knocks electrons loose in both layers. Because of the opposite charges of the layers, the electrons want to flow from the n-type layer to the p-type layer, but the electric field at the P-N junction prevents this from happening. The presence of an external circuit provides the escape path for electrons in the n-type layer to travel to the p-type layer. Extremely thin wires running along the top of the n-type layer provide the external circuit and the electrons flowing through this circuit provide the current.
Because the amount of power produced by a single solar cell is relatively small, one to two watts, designers group solar cells to form modules (panels) that supply a more useful level of voltage, current, and power. Solar cells may be connected in series to produce higher voltages. This is done by connecting the positive terminal of one cell to the negative terminal of the next cell. Cells may also be connected in parallel to produce more current. This is done by connecting the positive terminal of the first cell to the positive terminal of the next cell, and the negative terminal of the first cell to the negative terminal of the second cell.
This kind of solar cell is called a crystalline silicon cell. They are the dominant technology in the solar marketplace, accounting for about 90% of the installed market at the end of 2011. The efficiency of crystalline solar cells ranges from about 15% to a high of 23% which is very, very good. See the Solar Efficiency Limits page. Efficiency is defined as the electrical energy converted by the cell compared to the energy of the sunlight striking the surface of the cell.
Thin Film Solar Cells
Some newer types of solar cells are made from thin films of semiconductors chemically vapor deposited (CVD) or sputtered on glass or metal. However, thin film cells are not as efficient as silicon cells. The semiconductor materials in a thin film cell are just a few microns (millionths of a meter) thick, whereas crystalline silicon cells are 100 times or more thicker. If the wavelength of incoming light is longer than the thickness of the cell, it most likely will not be absorbed. This means that wavelengths in the infrared part of the spectrum will be weakly absorbed. Hence, thin film cells convert only 8 to 12% of incoming light versus 15 to 23% compared to crystalline silicon cells. However, thin film cells are considerably cheaper to make because they use only 1 or 2 percent of the expensive semiconductor material of a crystalline silicon cell.
This is a huge advantage in system cost. Because deposition systems can deposit materials on large surfaces, modules (panels) are made of much larger cells, typically about 2 feet by 4 feet, and only one cell per panel. These panels are fairly robust and can operate in a wide temperature range and a variety of light conditions, including dawn and dusk. Because thin film panels are less efficient, more are required to generate a given amount of electricity. Hence space is a consideration in the decision as to which technology is chosen.
Cadmium Telluride (CdTe)
The most significant vendor using thin-film cadmium telluride technology is First Solar, the largest manufacturer of solar modules in the world, headquartered in Tempe, Arizona. First Solar has come on very strong since 2006 due to its low module manufacturing cost per watt ($.73 as of Q4 2011). First Solar had about 7% of the world market share as measured by watts installed in 2011. Another company making CdTe solar panels is Abound Solar located in Loveland, Colorado.
Cadmium telluride (pictured above) is a semiconductor that is made from cadmium and tellurium. In general, the PV principles of converting light into electrical energy are the same as silicon cells. CdTe modules are in the range of 12% to 14% efficient versus 13% to 20% for crystalline silicon modules. CdTe has an optimum absorption profile (band gap) for the light spectrum of sunshine which allows it to obtain better performance in dim lighting. On the other hand, since CdTe cells are generally not as efficient as silicon cells, CdTe requires more total surface area to produce a given amount of electricity. This translates into more land, more inverters, etc. Hence this technology is used more in the massive utility market where cost is king and land is plentiful, whereas crystalline silicon is used more in the residential and commercial roof markets where space is king.
CIGS (Copper Indium Gallium Diselenide) Cells
Another type of thin film solar cell is made from Copper Indium Gallium diselenide, CIGS for short (pronounced Sigs). This is noteworthy because the semiconductor material can be deposited on a flexible base or substrate. The following figure is a cell from Global Solar Energy Inc. located in Tucson, Arizona. Global Solar uses stainless steel as a substrate. Although much smaller than the normal Cadmium Telluride market, CIGS technology is breaking into new markets in what is called the building-integrated photovoltaic (BIPV) market. Unlike conventional PV products such as solar panels, which are an add-on to say a roof, BIPV is manufactured directly into building materials, such as roof shingles, and installed during the building's construction stage. With PV solar cells built right into walls, roofs, and glass, the building material itself can generate the electricity needed to sustain the building’s needs. This is indeed a new exciting breakthrough for solar electricity.
CIGS cells have a better efficiency than other thin film technologies by about 2%. Every 1% of efficiency represents about a 6% overall cost reduction due to less land, modules, inverters, labor, etc. So a 2% efficiency lead would be about a 12% cost savings, not insignificant. CIGS also employs low-cost deposition methods that are an alternative to expensive vacuum deposition processes.
CIGS solar cells are expected to pass cadmium telluride in efficiency. In theory, both CIGS and CdTe solar cells can achieve a maximum efficiency of about 30 %. In real-world terms, however, CIGS is expected to come out on top. A more practical real-life best industry efficiency is expected to be about 25%.
Computing giant IBM announced a deal with Japanese semiconductor equipment manufacturer, Tokyo Ohka Kogyo (TOK) to make thin-film solar cells from CIGS. Neither IBM nor TOK plans to manufacture the solar cells themselves, rather, they are developing technology that will be licensed to solar manufacturing companies. IBM's CIGS technology came out of its Research Division and they believe that it can achieve 15% efficiency in production. IBM's manufacturing process calls for the chemicals to be dissolved in a liquid and then dried. It does not require a vacuum, does not require as much energy to run as standard CIGS techniques, and is a faster process.
Solar Efficiency Limits
The maximum theoretical efficiency of a perfect solar cell using a p/n junction to extract electrical power was first calculated by William Shockley and Hans Queisser in 1961 It is now known as the Shockley Queisser (SQ) Limit. A solar cell's energy conversion efficiency is the percentage of power converted from sunlight to electrical energy under "standard test conditions" (STC). The STC conditions approximate solar noon at the spring and autumn equinoxes in the continental United States with the surface of the solar cell perpendicular to the sun.
The modern SQ Limit calculation is a maximum efficiency of 33% for any type of single junction solar cell. The original calculation by Shockley and Queisser was 30% for a silicon solar cell. Current maximum theoretical solar cell efficiencies vary by the band gap of the semiconductor material used for the p/n junction as shown on the left (see P/N Junction and Band Gaps page). The best modern production silicon cell efficiency is 23% at the cell level and 20% at the module level as presented by SunPower in May 2010. In the laboratory, the record solar cell efficiency for monocrystalline silicon is held by the University Of New South Wales in Sydney, Australia at 25%.
There are some assumptions associated with the SQ Limit that restrict its general applicability to all types of solar cells. Although there are numerous programs underway to find ways around the SQ Limit, it is still applicable to 99.9% of the solar cells on the market today. The critical assumptions are:
All About Silicon
The Silicon Atom

The Silicon Lattice

Creating Silicon Wafers

The ingot can be one to two meters in length depending on the amount of silicon in the crucible. This process is normally performed in an inert atmosphere, such as argon, and in an inert chamber. A cutting machine designed to slice very hard silicon uses a multi-wire diamond saw. This device is especially important in the silicon solar cell industry to cut the ingots into very thin wafers 200 microns (millionths of a meter) or so thick, and some as thin as 160 microns. These extremely thin wafers are very brittle and are easily broken. Extreme care is necessary in the handling of these wafers to prevent damage.
Crystalline Silicon Solar Cells
The Photovoltaic Effect

To induce the "built-in electric field" within a PV cell, two layers of differing silicon are placed in contact with one another. One layer is an "n-type" material with an abundance of electrons, which have a negative electrical charge. The other layer is a "p-type" material with an abundance of "holes," which have a positive electrical charge. The top layer is "doped" with phosphorus, which bonds with the silicon to create a negative charge (extra electrons). The bottom layer of the PV cell is usually "doped" with boron, which bonds with the silicon to create a positive charge (extra holes).
The "dopant," which is the introduced element, has either three or five valence electrons—which is one less or one more than silicon's four. Substituting a phosphorus atom (with five valence electrons) for a silicon atom in a silicon crystal leaves an extra unbonded electron that is relatively free to move around the crystal. Substituting a boron atom (with three valence electrons) for a silicon atom in a silicon crystal leaves a hole (missing electron) that is relatively free to move around the crystal.
When n- and p-type silicon come into contact, the two semiconductors behave like a battery, creating the "built-in electric field", or voltage, at the surface where they meet called the "p/n junction". The voltage causes electrons to move towards the negative surface, where they become available to the external electrical circuit. At the same time, the holes move in the opposite direction, toward the positive surface, where they await incoming electrons. When the sun's photons enter the semiconductor, some of the photons with the "right amount" of energy collide with atoms, and free negative electrons and free positive holes are created. The "right amount" of energy is called the "band gap" energy and it varies from one semiconductor material to another. Given the electric field, the free negative electrons go in one direction and the free positive holes go in the other creating a current of electricity. The p/n junction is the key instrument in the creation of electricity by a solar cell.
Crystalline Silicon Cell Structure
A typical solar cell consists of a glass or plastic cover, an anti-reflective layer, a front contact to allow electrons to enter a circuit, a back contact to allow them to complete the circuit, and the semiconductor layers where the electrons begin and complete their journey.

Because the amount of power produced by a single solar cell is relatively small, one to two watts, designers group solar cells to form modules (panels) that supply a more useful level of voltage, current, and power. Solar cells may be connected in series to produce higher voltages. This is done by connecting the positive terminal of one cell to the negative terminal of the next cell. Cells may also be connected in parallel to produce more current. This is done by connecting the positive terminal of the first cell to the positive terminal of the next cell, and the negative terminal of the first cell to the negative terminal of the second cell.
This kind of solar cell is called a crystalline silicon cell. They are the dominant technology in the solar marketplace, accounting for about 90% of the installed market at the end of 2011. The efficiency of crystalline solar cells ranges from about 15% to a high of 23% which is very, very good. See the Solar Efficiency Limits page. Efficiency is defined as the electrical energy converted by the cell compared to the energy of the sunlight striking the surface of the cell.
Thin Film Solar Cells

This is a huge advantage in system cost. Because deposition systems can deposit materials on large surfaces, modules (panels) are made of much larger cells, typically about 2 feet by 4 feet, and only one cell per panel. These panels are fairly robust and can operate in a wide temperature range and a variety of light conditions, including dawn and dusk. Because thin film panels are less efficient, more are required to generate a given amount of electricity. Hence space is a consideration in the decision as to which technology is chosen.
Cadmium Telluride (CdTe)
The most significant vendor using thin-film cadmium telluride technology is First Solar, the largest manufacturer of solar modules in the world, headquartered in Tempe, Arizona. First Solar has come on very strong since 2006 due to its low module manufacturing cost per watt ($.73 as of Q4 2011). First Solar had about 7% of the world market share as measured by watts installed in 2011. Another company making CdTe solar panels is Abound Solar located in Loveland, Colorado.

CIGS (Copper Indium Gallium Diselenide) Cells


CIGS solar cells are expected to pass cadmium telluride in efficiency. In theory, both CIGS and CdTe solar cells can achieve a maximum efficiency of about 30 %. In real-world terms, however, CIGS is expected to come out on top. A more practical real-life best industry efficiency is expected to be about 25%.
Computing giant IBM announced a deal with Japanese semiconductor equipment manufacturer, Tokyo Ohka Kogyo (TOK) to make thin-film solar cells from CIGS. Neither IBM nor TOK plans to manufacture the solar cells themselves, rather, they are developing technology that will be licensed to solar manufacturing companies. IBM's CIGS technology came out of its Research Division and they believe that it can achieve 15% efficiency in production. IBM's manufacturing process calls for the chemicals to be dissolved in a liquid and then dried. It does not require a vacuum, does not require as much energy to run as standard CIGS techniques, and is a faster process.
Solar Efficiency Limits
The maximum theoretical efficiency of a perfect solar cell using a p/n junction to extract electrical power was first calculated by William Shockley and Hans Queisser in 1961 It is now known as the Shockley Queisser (SQ) Limit. A solar cell's energy conversion efficiency is the percentage of power converted from sunlight to electrical energy under "standard test conditions" (STC). The STC conditions approximate solar noon at the spring and autumn equinoxes in the continental United States with the surface of the solar cell perpendicular to the sun.

The modern SQ Limit calculation is a maximum efficiency of 33% for any type of single junction solar cell. The original calculation by Shockley and Queisser was 30% for a silicon solar cell. Current maximum theoretical solar cell efficiencies vary by the band gap of the semiconductor material used for the p/n junction as shown on the left (see P/N Junction and Band Gaps page). The best modern production silicon cell efficiency is 23% at the cell level and 20% at the module level as presented by SunPower in May 2010. In the laboratory, the record solar cell efficiency for monocrystalline silicon is held by the University Of New South Wales in Sydney, Australia at 25%.
There are some assumptions associated with the SQ Limit that restrict its general applicability to all types of solar cells. Although there are numerous programs underway to find ways around the SQ Limit, it is still applicable to 99.9% of the solar cells on the market today. The critical assumptions are:
- One semiconductor material (excluding doping materials) per solar cell.
- One P/N junction per solar cell.
- The sunlight is not concentrated - a "one sun" source.
- All energy is converted to heat from photons greater than the band gap.
Post a Comment:
You may also like:
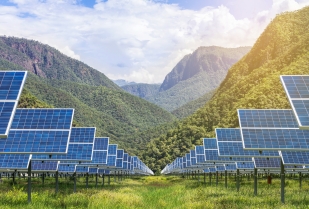
Category
Featured Articles
Expanding Research on Solar Energy ...
The application fields of solar energy are very wide, covering many fields such as the photonic industry, new energy photothermal ...
Exploring Concentrated Solar Power ...
Concentrated Solar Power (CSP) systems use very different technology than photovoltaic systems. CSP systems use the sun as the ...
Solar Cell Manufacturing Process
Solar cells are made of various materials, the most common of which include silicon, indium gallium, cadmium selenide, etc. These ...
The Evolution of Grid Electricity ...
"Electricity" cannot be stored on the grid; generation must be approximately equal to consumption at all times. However, ...
Solar Activity: Sunspots, Magnetism & ...
Solar activity refers to a series of complex phenomena in the solar atmosphere, including sunspots, flares, prominences, coronal ...