Decoding Stirling Engine Designs
Stirling Engines
The original Stirling engine was developed in 1816 by Robert Stirling as an alternative to the early steam engine which tended to explode. However, its practical use was confined to low power domestic applications. The Stirling engine is noted for its high efficiency (up to 40%), quiet operation, and the ease with which it can use almost any heat source, in this case the sun's heat. This compatibility with renewable energy has become significant because of concerns for the US addiction to oil, the carbon footprint, and climate change consequences. The Stirling engine is a waterless CSP technology.
Over the years many different versions of the Stirling engine have been devised. Initially, the simplest version, the Alpha Sterling engine, will be explained. Afterwards a more modern version, the Siemens configuration with four cylinders will be explained. There are also several versions in between.
The Alpha Stirling Engine
An Alpha Stirling engine contains two
pistons in separate cylinders, one hot and one cold. The hot cylinder is
situated inside the high temperature heat exchanger and the cold cylinder is
situated inside the low temperature heat exchanger. The working gas (usually
hydrogen) inside both cylinders comes in contact with the hot cylinder walls
which are heated from an external source. The gas is raised to a temperature of
approximately 650ºC. The picture on the right is a simplified Stirling engine in operation.
1. The hot gas (red) expands and
pushes the hot piston to the end of its travel in the cylinder. The gas
expansion continues in the cold cylinder (blue), which is 90° behind the hot
piston in its cycle, extracting more energy from the hot gas.
2. The total gas is now at its
maximum volume in both cylinders. The hot cylinder piston begins to move most of
the gas into the cold cylinder, where it is cooled and the pressure drops.
3. Almost all the gas is now in
the cold cylinder and cooling continues. The cold piston, powered by the
flywheel momentum (or other piston pairs on the same shaft) compresses the remaining
gas in the hot cylinder.
4. The total gas reaches its
minimum volume, and it will now begin to expand in the hot cylinder where it is
being heated once more. The expanding hot gas will drive the hot piston through
its power stroke as the overall cycle begins anew.
Add a Regenerator
In a real Sterling engine, a lot of energy
is lost in the gas transfer between the two cylinders. Hence a major
innovation, called the "regenerator", also invented by Robert
Stirling, is used to conserve energy and improve efficiency. The regenerator is
an internal heat exchanger and temporary heat storage unit placed between the
hot and cold cylinders such that the working fluid passes through it first in
one direction and then back in the other. Its function is to retain some of the
heat within the system that would otherwise be exhausted to the atmosphere. It
does this at intermediate temperatures between the minimum and maximum cycle
temperatures. The primary effect of regeneration is to greatly increase the
thermal efficiency by 'recycling' internal heat which would otherwise pass out
of the engine. A typical regenerator design is a stack of fine metal wire
meshes with low flow resistance and with the wire axes perpendicular to the gas
flow to reduce conduction in that direction.
The Siemens Stirling Engine
The Alpha engine can be compacted into a
small multiple cylinder configuration, enabling very high-power output. A
schematic diagram of the "Siemens" configuration is shown below. The Siemens configuration does not use two separate pistons, but rather
uses the front and back side of one piston called a double-acting piston. With
a double-acting piston, the expansion space of the front side of one piston is
connected to the compression space of the back side of the adjacent piston
through the in-line heater, regenerator, and cooler. The Siemens configuration
involves four cylinders each with a double-acting piston 90 degrees out of
phase with the next cylinder. The Siemens configuration greatly improves the
engine efficiency over the original alpha arrangement. These engines have the
power piston connected to the crankshaft by a second connecting rod, which is
itself in another small cylinder to eliminate the lateral forces from the
crankshaft from putting pressure on the engine cylinder walls. This arrangement
is called a "crosshead". A seal is used between the cross-head and
piston to separate the high-pressure area from the low-pressure zone. This
allows the crosshead surfaces to stay lubricated in the low-pressure area while
preventing fouling in the high-pressure engine system.
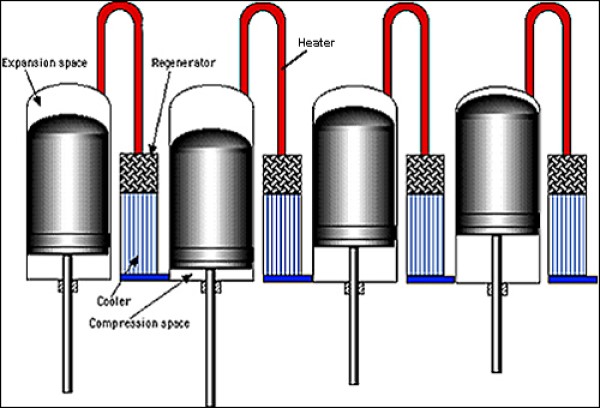
Post a Comment:
You may also like:
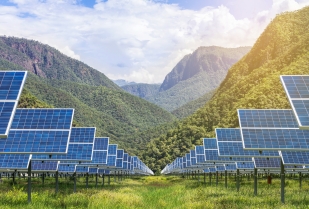